How to use slitting machine to achieve efficient slitting and slitting of materials?
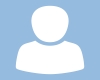
Posted by delishslitter
from the Business category at
22 Apr 2025 02:59:04 am.
1. Equipment selection and configuration
• Matching material characteristics: Choose the appropriate slitting machine type (such as round knife slitting, cantilever slitting, laser slitting, etc.) according to the type of material (film, paper, metal foil, composite material, etc.).
• Tool selection:
◦ Tungsten carbide or diamond tools are suitable for high hardness materials.
◦ The angle and sharpness of the cutting edge of the tool should be checked regularly to avoid burrs or delamination.
• Tension control system: Equipped with high-precision magnetic particle or servo tension control to ensure that the material has no tensile deformation or wrinkles during the slitting process.
• Automation integration: Install automatic web correction, on-line inspection (e.g. CCD vision system) and waste edge suction device to improve efficiency.
2. Optimization of process parameters
• Slitting speed: Adjust the speed according to the thickness and hardness of the material to avoid uneven cuts or overheating of the tool due to too fast speed.
• Slitting width accuracy:
◦ Use a high-precision CNC system to set the slitting size to ensure that the tolerance is within ±0.1mm.
◦ For thin materials (such as lithium battery separators), non-contact slitting (air float slitting) is required to reduce deformation.
• Tension adjustment: Differential tension is set for different material stages (unwinding, slitting, winding), such as:
◦ Unwinding tension: 10~50N (adjusted according to the tensile strength of the material).
◦ Rewinding tension: slightly lower than the unwinding tension to prevent the material from curling too tightly.
3. Operational Specifications
• Pre-run checks:
◦ Confirm the parallelism of the tool installation to avoid slitting deviation.
◦ Clean up impurities on the roll surface to prevent scratches on the material.
• Trial Cutting & Adjustment:
◦ Test cutting at low speed, check the quality of the slitting edge, and adjust the tool pressure and angle.
◦ For multi-layer composites, the slitting depth should be verified to avoid damage to the bottom layer.
• Rewinding control:
◦ Using taper tension control, the tension gradually decreases during winding (e.g., from 100 N to 60 N) to prevent the inner material from being extruded and deformed.
4. Quality control and testing
• On-line monitoring: Detect defects such as burrs and wavy edges on the slitting edge by infrared sensor or ultrasonic.
• Sampling test: 5~10 samples are taken from each batch, the width and verticality are measured, and the microscopic quality of the incut is observed with a microscope.
• Data recording: record parameters such as slitting speed, tension, tool wear cycle, etc., and establish a process database.
5. Maintenance and tool management
• Regular Maintenance:
◦ Lubricate rails and bearings every 8 hours.
◦ Change hydraulic oil or check air tightness every 500 hours.
• Tool maintenance:
◦ Sharpen the tool after 50 km of material per slitting (or adjust according to the wear coefficient of the material).
◦ Use a tool setter to ensure consistent slitting across multiple sets.
• Failure Prevention:
◦ Install vibration sensor to monitor spindle abnormality and warn in advance.
6. Efficiency improvement techniques
• Batch slitting: Centralized production for orders of the same specification to reduce tool change and debugging time.
• Quick mold change system: with hydraulic locking tool holder, the changeover time can be shortened to less than 10 minutes.
• Energy consumption optimization: Variable frequency drive motor is 15%~20% energy-saving compared with traditional motor.
Common Problem Solving
• Flashing problems: Check the sharpness of the tool or increase the pressure on the roller.
• Uneven slitting width: calibrate the parallelism of the guide rollers or check the encoder of the CNC system.
• Material Warpage: Adjust the winding tension or add a static eliminator.
Through the above measures, the efficiency of the slitting machine can be increased by 30%~50%, and the rejection rate can be controlled below 0.5%. The key is to dynamically adjust the process according to the material properties and establish standardized operating procedures (SOPs).
Tags: slitting machine
0 Comments