Dust-free slitting + online quality inspection! Ribbon slitting machine solves the pain points of the industry
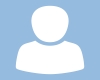
Posted by delishslitter
from the Agriculture category at
17 Apr 2025 06:46:07 am.
Analysis of industry pain points
1. Dust pollution
◦ The traditional slitting machine is easy to produce carbon crumbs, pollute the workshop environment, and affect the equipment life and product yield.
2. Low slitting accuracy
◦ Ribbon edges are burred and unevenly wide, resulting in jamming or breakage during printing.
3. Quality inspection lags
◦ Relying on manual sampling, which is inefficient and easy to miss defects (such as scratches, bubbles, and uneven slitting).
Solution: dust-free slitting + online quality inspection
1. Dust-free slitting technology
• Electrostatic adsorption and dust removal system
An ionizer is installed near the slitting blade to adsorb the toner generated during cutting, and with a micro dust collection device, it can be cleaned instantly.
• Low temperature slitting process
Cryogenically cooled blades (e.g. PCD) are used to reduce toner scattering caused by frictional heat.
• Closed slitting module
The semi-sealed slitting chamber is designed with an airflow circulation filtration system (HEPA filter) to prevent dust from escaping.
2. High-precision slitting control
• Servo drive + tension control
The high-precision servo motor cooperates with the closed-loop tension control system to ensure that the slitting width error ≤± 0.1mm.
• Laser-guided positioning
The laser calibrates the slitting path in real time to avoid material misalignment.
• Adaptive blade wear compensation
The blade status is monitored by a pressure sensor and the cutting depth is automatically adjusted.
3. Online intelligent quality inspection
• Machine vision inspection
◦ Defect identification: high-speed industrial camera + AI algorithm, real-time detection of scratches, bubbles, and stains on the surface of the ribbon.
◦ Edge detection: The line scan camera scans the slitting edge and identifies burrs or sawtooth with an accuracy of up to 0.05mm.
• Closed-loop data feedback
The inspection results are fed back to the slitting system in real time, which automatically adjusts parameters or marks defective segments (e.g. inkjet marking).
• SPC statistical analysis
Record slitting quality data, generate trend reports, and assist in process optimization.
Core Benefits:
• Yield improvement: 100% full inspection of online quality inspection, and the rate of defective products is reduced to less than 0.5%.
• Reduce costs and increase efficiency: Reduce the cost of manual cleaning and re-inspection, and increase production capacity by 30%+.
• Environmental compliance: Dust-free design meets ISO14644 clean room standards.
Application scenarios
• High-end ribbon production: such as electronic labels, medical consumables and other fields with high cleanliness requirements.
• Automated production line integration: It can be linked with upstream coating machines and downstream packaging machines to create a smart factory.
Technology extension
• AI predictive maintenance: Reduce downtime by predicting blade life with vibration sensors and slitting data.
• Digital twin: Virtual debugging optimizes slitting parameters and shortens the development cycle of new products.
Through the integrated design of "dust-free slitting + online quality inspection", the ribbon slitting machine can significantly solve the pain points of the industry and promote the label printing industry to upgrade to intelligence and green.
Tags: ribbon slitting machine
0 Comments