How to achieve ±0.1mm ultra-precision slitting of ribbon slitting machine? Analysis of key functions
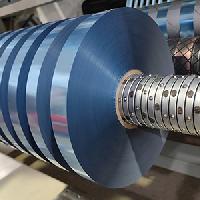
Posted by slittermachine
from the Business category at
09 Apr 2025 02:05:39 am.
1. Core challenges and influencing factors of accuracy
1. Ribbon characteristics:
◦ The material is soft (such as wax-based, mixed-based, resin-based), easily stretched or deformed, and sensitive to tension.
◦ Multi-layer composite structure (such as PET substrate + coating) requires that the incision is free of delamination and burrs.
2. Precision Interference Sources:
◦ Mechanical vibration, tension fluctuations, tool wear, feeding slippage, etc.
Second, the key technology to achieve ±0.1mm ultra-precision
1. High rigidity mechanical structure design
• Precision guide rails and lead screws:
C-level or higher precision linear guide + ball screw (axial clearance ≤0.05mm) is used to ensure that the tool holder moves without return error.
• Split turret:
The upper and lower tool axes are driven independently, and the tool pitch (resolution 0.01mm) is fine-tuned through the servo motor to adapt to different ribbon thicknesses.
• Air Bearing Support:
Non-contact support is used for thin ribbons (e.g. 6 μm) to avoid deformation of the material under compression.
2. Intelligent tension control system
• Multi-stage closed-loop tension control:
◦ Unwinding (magnetic powder brake) + traction (servo motor) + winding (vector frequency conversion motor) three-stage independent tension control, fluctuation range ≤± 0.5N.
◦ Real-time feedback: through tension sensor or floating roller detection, PLC dynamic adjustment.
• Taper Tension Algorithm:
When winding, the tension is automatically reduced with the increase of the roll diameter to prevent the inner layer from being extruded and deformed.
3. Ultra-precision cutting system
• Tool selection and configuration:
◦ Round knife cutting: tungsten carbide blade (mirror polished, Ra ≤0.2μm), cutting edge angle 30°±1°, life ≥ 1000km.
◦ Ultrasonic cutting (optional): High-frequency vibration cutting, suitable for highly viscous resin-based ribbons, reducing burrs.
• Dynamic tool setting technology:
The laser displacement sensor monitors the knife gap in real time and automatically compensates for tool wear (e.g. 0.005mm per 10km cut).
4. High-precision correction and feeding
• CCD Vision Correction:
The line scan camera scans the edge of the ribbon, the positioning accuracy is ± 0.03mm, and the linkage servo motor is horizontally adjusted (response time≤ 10ms).
• Servo-direct drive feeding:
Eliminate the traditional gear drive, directly drive the feed roller, the encoder resolution ≤ 1μm, and eliminate the backlash error.
5. Environmental and vibration control
• Constant temperature workshop:
The temperature fluctuation ± within 1°C to avoid thermal expansion and contraction of the material.
• Active Vibration Damping Base:
Gas spring or magnetic levitation vibration isolation to reduce ground vibration conduction (e.g., ≤0.01g).
3. Intelligent auxiliary functions
• Automatic Calibration System:
Automatically calibrate the tool, tension sensor and guiding reference after start-up, reducing manual adjustment time.
• Big Data Optimization:
Historical cutting parameters (e.g., optimal tension and speed for different ribbon models) are recorded, and the AI recommends process recipes.
• Remote Diagnostics:
Real-time monitoring of equipment status via 5G/industrial Internet to warn of potential failures (e.g. insufficient tool life).
Fourth, practical application cases
• After a label material manufacturer upgrades its slitting machine with the above technology:
◦ Slitting width tolerance increased from ±0.3mm to ±0.08mm;
◦ Scrap rate reduced from 2.5% to 0.3%;
◦ The speed reaches 120 m/min (originally 80 m/min).
5. Key points of maintenance and operation
1. Routine Maintenance:
◦ Clean rails and optical sensors per shift;
◦ Weekly inspection of tool wear (microscopic observation of cutting edges).
2. Operational Specifications:
◦ The ribbon needs to be stored at constant temperature and humidity (23°C±2°C, RH50%±5%);
◦ Allow to stand for more than 4 hours before slitting to eliminate internal stress.
6. Suggestions for equipment selection
• Priority Configuration:
◦ Brand servo system (such as Yaskawa, Panasonic) + high-precision encoder;
◦ PLCs that support the EtherCAT bus (e.g. Beckhoff, Siemens) ensure real-time performance.
• Verification Criteria:
Require the supplier to provide a third-party test report (e.g., laser interferometer measurement repeatability).
Through the integration of the above technologies, the ribbon slitting machine can achieve ultra-precision slitting of ±0.1mm, which can meet the needs of high-end electronic labels, medical barcodes and other demanding scenarios. The core lies in the collaborative optimization of mechanical stability, dynamic control accuracy and intelligent compensation.
Tags: ribbon slitting machine
0 Comments