What structure of aluminum cold foil is suitable for pharmaceutical packaging?
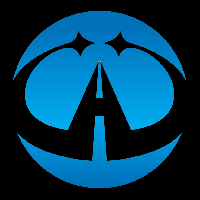
Posted by hwalu
from the Agriculture category at
11 Nov 2024 07:50:53 am.
Cold-formed pharmaceutical packaging
Aluminum foil is a good pharmaceutical packaging material, while cold-formed aluminum foil is a pharmaceutical packaging material with more outstanding performance. For pharmaceutical packaging, the aluminum cold foil commonly used is a laminated structure that combines the protective properties of aluminum with additional layers to achieve functions such as barrier protection, printability, and sealing.
Cold-formed structure suitable for pharmaceutical packaging
Typical cold foil structure for pharmaceuticals, standard aluminum cold foil for pharmaceutical packaging may consist of the following layers:
a. Polyester (PET) film layer (12–25 microns)
– Purpose: used as a base carrier film to provide mechanical strength and printing surface.
– Features: high dimensional stability, smooth printing surface, good tear resistance.
– Thickness: 12–25 microns, depending on the requirements for flexibility and strength.
b. Adhesive layer (1–3 microns)
– Purpose: bond polyester film to aluminum foil.
– Features: Heat activated adhesive or pressure sensitive adhesive that ensures a secure bond without compromising the barrier properties of the foil.
c. Aluminum foil layer (6-9 microns)
– Purpose: Acts as the primary barrier layer to protect the drug from moisture, light, oxygen and other contaminants.
– Features: High barrier to gases and moisture, light reflective and non-toxic.
– Thickness: 6-9 microns (7mic,9mic)is the standard thickness for cold foil applications for pharmaceuticals.
d. Heat seal coating/primer layer (1-5 microns)
– Purpose: Provides a surface that can be heat-sealed to blister packs or other substrates.
– Features: This layer is compatible with the sealing layer of PVC or PVDC blister films. It ensures a secure seal without affecting the drug inside.
– Type: Typically a heat seal lacquer or primer that adheres well to PVC, PVDC or other common blister substrates.
Enhanced cold foil structure
In some cases, aluminum cold foil may have additional layers for better performance:
e. Protective coating (optional, 1-2 microns)
– Purpose: Enhance the abrasion and chemical resistance of the foil.
– Features: Provide an additional barrier, especially important for highly sensitive pharmaceuticals.
Key to cold aluminum for pharmaceutical packaging
Cold-formed aluminum foil as the outer packaging of pharmaceuticals needs to have the characteristics of protecting the pharmaceuticals and blocking external factors, so the key considerations for pharmaceutical cold foil packaging are four aspects:
1. Barrier: The aluminum foil layer provides an excellent barrier against moisture, oxygen and UV rays to protect the stability and efficacy of the drug.
2. Printability: The PET film layer enables high-quality label and brand printing, which is critical for regulatory compliance and product identification.
3. Compatibility: The structure must be compatible with pharmaceutical packaging machines and meet regulatory requirements (e.g. FDA, EMA).
4. Sealing performance: The heat-seal coating must ensure a strong seal with the blister packaging substrate (e.g. PVC, PVDC-coated PVC or Aclar® laminate).
Typical cold foil thickness range:
– PET film: 12–25 microns
– Adhesive layer: 1–3 microns
– Aluminum foil: 6–9 microns
– Heat seal coating: 1–5 microns
This structure achieves a balance between barrier protection, printability and sealing efficiency. Cold-formed aluminum is very suitable for pharmaceutical packaging materials due to its orderly structure, excellent ductility, excellent barrier properties, good sealing properties and many other advantages.
Tags: aluminum foil
0 Comments