The influence of ribbon slitting technology on ribbon quality
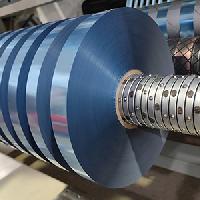
Posted by slittermachine
from the Business category at
08 Oct 2024 02:08:33 am.
Each roll of high-quality ribbons with good compatibility and clear printing results is the result of excellence in the slitting process. In addition to advanced slitting equipment, ribbon slitting machine manufacturers with high-quality ribbon slitting capabilities also need a clean and dust-free slitting workshop environment and a group of high-quality slitting technical personnel.
First, Advanced slitting equipment
The width is measured in millimeters, and the length of the ribbon is hundreds or even thousands of meters, to quickly and accurately cut it into small rolls, it is impossible to achieve without advanced ribbon slitting machine. The production speed of the previous generation ribbon slitting machine is 30% slower, and the width ± tolerance of the slitting ribbon cannot be accurately controlled. The improved and more advanced slitting equipment can not only perfectly meet the needs of fast slitting, but also strictly control the quality of ribbon slitting. Among them, the tension of the ribbon slitting machine and the flatness of the ribbon when rewinding are the key points of production control.
1. Tension control during ribbon slitting:
• When the tension is too large, the PET base film of the ribbon will be tensile and damaged, which will lead to physical changes in the ink layer attached to the base film, which is easy to produce quality problems of ribbon powder, affect the printing effect, and even produce serious quality problems of contaminating the goods with the detached toner.
• If the tension of the ribbon is not enough during slitting, the ribbon is prone to wrinkles, resulting in white lines, indentations and other poor printing during printing. Loose ribbon rewinding tension can also lead to quality problems such as die deviation and ribbon slippage during transportation or installation.
• After the installation of each newly purchased ribbon slitting machine, a large amount of debugging work is required to find the most suitable tension range during the debugging process, and this tension interval data is the key data for technicians to maintain the equipment in the later stage.
Second, Flatness control during ribbon rewinding:
As we all know, the ribbon base belt is a kind of PET film, and during the printing process, because the ribbon printer will also adjust the tension, there will be a large tensile force between the supply shaft and the recycling shaft, and the force of the ribbon should be uniform so that it is not easy to break. Therefore, when the ribbon is rewound, the ribbon must be completely flat and parallel to the die, so that the edge of the ribbon will be evenly stressed during the printing process and will not be easy to break. If the stress point is at the edge of the ribbon, the ribbon can easily break. The uneven rewinding of the ribbon will also lead to wrinkles during the printing process, and it is easy to have white lines, indentations and other printing defects.
Third, Clean and dust-free slitting environment
In addition to requiring excellent production equipment, a roll of high-quality ribbon also comes from a clean production environment. In the process of ribbon production, it is easy to adsorb dust in the air, and the ribbon polluted by dust is easy to produce bad white spots when printing, and the slitting workshop of the ribbon needs to be equipped with dust-free ground, while maintaining appropriate temperature and humidity to reduce the impact of dust on production.
Third, the quality of professional personnel
Professional ribbon slitting technicians should not only be proficient in operating equipment, but also have a serious and responsible attitude. Excellent products come from the unremitting pursuit of excellence.
Tags: ribbon slitting
0 Comments