Introduction of plastic roll film slitting machine
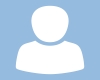
Posted by delishmachine
from the Business category at
10 Sep 2024 02:30:01 am.
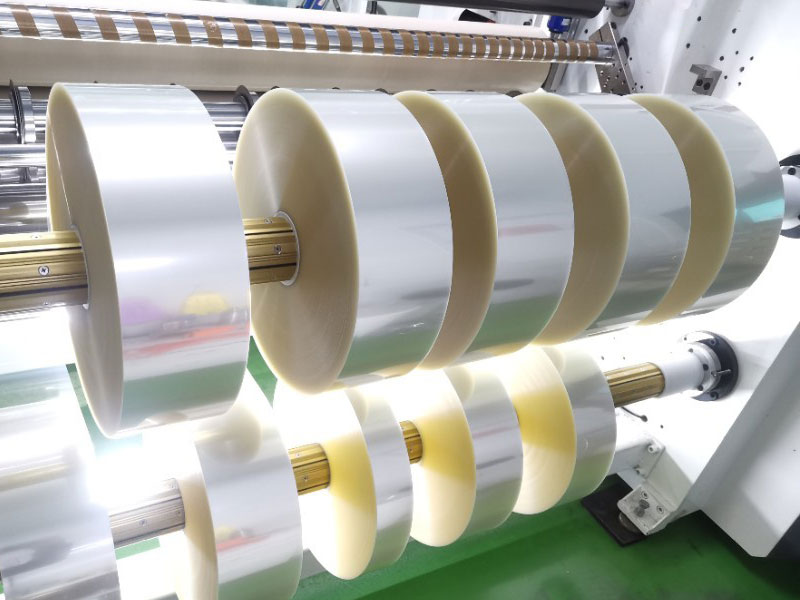
Plastic film slitting machine is a kind of flexible packaging equipment that can cut a wide plastic roll film into a lot of narrow strip film suitable for production needs, the plastic film slitting machine produced by Delish Machinery is often used to cut different sizes of film materials including aluminized film, BOPP film, CPP film, LDPE film, PP film, polyester film, PE film, PET film (ribbon) and so on, which are widely used in printing and packaging and related film composite industries.
Structure of plastic roll film slitting machine
The common plastic roll film slitting machine is composed of a mechanical part and an electrical part. The mechanical part mainly includes wide unwinding station, traction station, slitting station, narrow web winding station, hydraulic and braking system and so on. The plastic film material is released by the unwinding mechanism, and enters the slitting mechanism through a series of functional rollers such as flattening rollers, tension detection rollers, and deviation correction rollers, and the material is rewound into a film material that meets the specifications after slitting.
The electrical part mainly uses PLC as the core of the control system of the plastic film slitting machine, and all the switching quantities will be carried out in the operation process. Complete the command input through the touch screen of the man-machine interface, and set the operating parameters of the equipment. At the same time, with the help of relevant programs, the output of the PLC is controlled, the action of each component is controlled, and the functions of self-diagnosis, input sampling, and external equipment communication of the system are realized.
The main process of plastic roll film slitting machine
1. Roll film feeding: hoist the mother roll that needs to be slitted onto the unwinding rack of the slitting machine and lock the mother roll, if the unwinding mechanism adopts an inflatable shaft, the plastic roll film needs to be pushed to the appropriate position and inflated to tighten the coil. The rewinding spool is worn on the paper core that meets the specifications, and the loading process needs to pay attention to safety and ensure that the front and back of the material and the direction of rotation are correct.
2. Adjusting the knife process: adjust the knife distance according to the requirements and ensure that the knife edge direction is correct. The use of pneumatic pressure cutting round knife or razor slitting only needs to adjust the knife distance according to the requirements and lock, and check that the knife holder is not loose and the round blade rotates smoothly, so as not to affect the slitting quality. The use of round knife cutting method generally adjust the appropriate distance between the upper round knife and the lower round knife and align the middle of the lower knife groove, the gap between the upper and lower knives is generally about 2mm, too large slitting will have burrs, too small will damage the blade, if necessary, the bottom knife can be removed and re-arranged.
3. Film threading: Film threading is to distribute the plastic roll film on the guide roller of the equipment smoothly according to the process requirements of the material mother roll designed by the slitting machine. In the process of penetrating the film, it is necessary to correct the position of the edge, so that the material is in the center of the correction formation. At the same time, adjust the paper core on the reel to paste the slitted narrow material on the paper core and align it.
4. Coil film splicing: The film grafting process is when the slitting of the mother roll film material is completed for roll splicing. First of all, the new and old roll film materials are aligned and superimposed, and then placed on the film splicing table, and then the beading is opened to press the film. Use a paper cutter to cut off the excess material head neatly along the gap, and use tape or ultrasonic welding to bond it smoothly, paying attention to the joint part must be neat and wrinkle-free.
5. Film blanking: Blanking is the process of unloading the finished film coil material after slitting from the winding shaft. There are many ways to discharge the film slitting machine, and for lighter materials, the film roll is generally pushed out from the side of the unwinding shaft or the inflatable shaft is directly removed. For larger film rolls, a discharge frame or crane is generally used to assist in blanking. In addition, fully automatic discharge racks equipped with automatic translation mechanism are also increasingly used in plastic roll film slitting machines.
0 Comments