Quality issues in film slitting
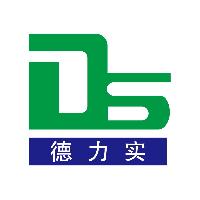
Posted by delishgroup
from the Business category at
10 Aug 2024 02:13:20 am.
The end face of the film coil is uneven
The first possibility is that the tracking problem of the correction electric eye should be carefully checked and adjusted to the status of the photoelectric tracking film. The second is that the winding tension is too small, which will also lead to the phenomenon of uneven film end face, which can be solved by directly adjusting the winding tension on the operation panel of the slitting machine. The third is that the film accumulates a large amount of static electricity during the winding process, resulting in adhesion or drift between layers. This requires the installation of passive or active anti-static devices on the slitting equipment to eliminate the effects of electrostatic electricity.
The film wrinkles during the slitting process
The first possibility is that the wrapping angle between the roller and the roll is too large to cause wrinkling, and the roller touches the roll and applies pressure during the slitting process, which can alleviate the vibration of the roll and the tissue air entering the coil. When the diameter of the roller is too large, a large bag angle is formed between the film roll and the roller, and the air is easy to roll into the material to form longitudinal folds. This problem is eliminated when the roll diameter is continuously increased to a larger than the roll diameter. So the solution is to choose a larger diameter for the core or a smaller diameter for the roller. The second possibility is that the pressure of the pressure roller will increase with the increase of the diameter or slitting speed of the film roll, resulting in the loose inner diameter of the coil and the quality problem, so with the increase of the material diameter and slitting speed, the pressure of the pressure roll should be appropriately reduced.
In addition, film tension is also an important factor affecting the quality of slitting, excessive tension will cause the material to be stretched, and uneven transverse force will cause wrinkles. The tension is too small during slitting and winding, and it is easy to cause the phenomenon of film running and loosening. Therefore, as the diameter of the film roll increases, the tension should be set to gradually decrease, and too fast a decrease will also cause the film to slide between layers.
There are abrasions and slippery marks on the surface of the film roll
In the process of slitting and rewinding, when there is a foreign matter on the surface of the roller or when processing burrs, the surface of the material will be scratched and the quality problem will occur. Therefore, during the slitting process, the guide rollers of the equipment should be carefully inspected and cleaned. In addition, in the process of operation of some high-speed slitting machines, it is very easy to slip and rub the surface of the smooth roller to cause material damage, and the Delishi slitting machine generally chooses to wind the cork belt on the surface of the smooth roller to solve this problem, please refer to the article for details: The application of cork belt on the slitting machine, which will not be repeated here.
The film appears to be tendoned and curled
When slitting some film materials with large thickness tolerances, as the tolerance accumulates, the film roll will be bursting, and the solution is to add a small amount of sanitary slippery powder at the film winding position. When cutting some light and thin materials, the substrate is easy to curl inward to form curls, so consider increasing the curvature of the flattening roller and adding a small amount of sanitary slip powder to the film crimping position.
To control the quality of film slitting, it is necessary to adjust the slitting process in time according to the working conditions. In addition, the properties of different types of plastic films are also different, and the design of the slitting method will also be different.
Tags: film slitting
0 Comments