A brief description of the film slitting process
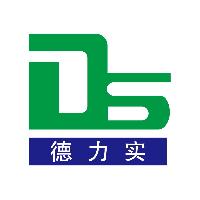
Posted by delishgroup
from the Business category at
09 Aug 2024 07:18:38 am.
The goal of film slitting
1. Slitting according to the width and length required by customers, and providing accurate specifications.
2. At the same time of slitting and unwinding, observe and re-inspect the material of the parent roll compounded in the previous process, and find quality problems in time.
3. After finding the problem, remove the defective materials in time, such as film staggering or composite printing defects, to improve product quality.
4. Set the optimal process parameters according to the characteristics of the film to achieve the best winding effect.
Film slitting process
Before starting the machine, it is necessary to carefully observe the appearance of the large master roll in the front pouring process, such as lamination or printing, especially to check the hardness and surface flatness of the mother roll to confirm whether it meets the slitting requirements. Then, fully familiarize yourself with the equipment status of the film slitting machine, check whether the mechanical parts and electrical parts of the slitting machine are in good working order, and whether the blades need to be replaced. Then install the parent roll to the winding shaft, adjust the blade spacing according to the width requirements, and fix the film according to the film walking diagram and start the slitting operation.
The process parameters of the film slitting machine should be determined according to the thickness of the film substrate, the physical properties of the material and other factors. Select the appropriate slitting process for different materials, such as adjusting tension, pressure, tension pressure gradient, correction factor, tension attenuation value, etc. Especially for some small size materials, the thickness itself is relatively thin, and it is easy to be damaged during the slitting process. Delishi Machinery requires operators not only to be very familiar with the material properties of different models, but also to constantly make practical adjustments in the operation process and select the optimal parameter combinations. In addition, it is necessary to have an understanding of the operating conditions of the equipment. For example, different slitting stations will have different degrees of wear and tear in the case of long-term use, and the stations with less wear will have higher accuracy and fewer streaks, and vice versa. On this basis, the operator should choose the right station to get the best out of the slitting equipment.
In actual operation, in order to increase the output of the staff and increase the economic benefits, the slitting speed is simply and rudely increased, ignoring the working conditions of the equipment and the performance of the film material. Under the high-speed operation of the film, due to the existence of some objective factors, such as the poor quality of the parent roll or paper core, or the accuracy of the equipment itself, it is extremely easy to have quality problems such as deviation, staggering or streaks. Therefore, whether the slitting speed can be controlled according to the requirements of the slitting process has become the key factor affecting the slitting quality. In addition, high-speed operation is easier for foreign objects to enter the film roll, and for some packaging film products used for food and drugs, it obviously does not meet the hygiene requirements. Therefore, manufacturers should find a balance between slitting speed and slitting quality.
To sum up, the process of film slitting must strictly follow the slitting process of specific materials in order to solve a series of quality problems in the slitting production process and ensure the stable quality of film slitting.
Tags: film slitting machine
0 Comments