Acquire the expertise required to choose the CNC machining center that will serve your purposes in t
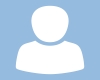
Posted by black
from the Technology category at
06 Mar 2023 12:57:57 am.
In general, machining centers are at their most effective when applied to the processing of components that exhibit the following characteristics:Workpieces that require the use of die casting a large number of distinct tools throughout the course of their processing are referred to as "multi-process intensive workpieces," and they are characterized by this characteristic. Taking advantage of the machine tool's high positioning accuracy makes it very convenient to implement for workpieces that have complicated positioning. For example, multi-hole machining is something that has a requirement for positioning accuracy, so taking advantage of the machine tool's high positioning accuracy is required. This is due to the fact that it satisfies the requirement for accurate positioning. Workpieces that have been developed for use in repetitive production can also be used successfully in one-off and small-batch manufacturing environments. A batch size is considered to be small if it contains one hundred items or fewer.
Additionally, despite the fact that the workpieces come in a wide variety of sizes and shapes, it is still possible to carry out group processing on them because they are sufficiently comparable to one another. On the machining center, complicated shape parts like molds, aviation parts, and other complex shape workpieces are able to process a wide variety of uniquely shaped parts with the assistance of automatic programming technology. This allows for greater flexibility in the design of the finished product. In the event that even the top surface needs to be worked on in a single clamping, a pentahedron machining center is a choice that can be taken into consideration as an option. With the assistance of the vertical small machining center, complex components such casting services as box heads, cylinder heads, flat cams, and other parts are easily machined.
It is for the purpose of processing large box and plate parts, such as those found in diesel locomotive cylinders, machining center columns and beds, printing wall panel machines, and other components that are comparable, that the machining center is used. The selection of CNC machining center specifications, in accordance with the size of the determined processing wire cutting workpiece, determines, in a corresponding manner, the worktable size of the required machine tool as well as the stroke of the three linear coordinate systems. This size of the workpiece is determined by the size of the processing wire cutting workpiece. In addition to this, it is very important to take into consideration the constraints that are imposed by the tool change space as well as the interference zone that is associated with each coordinate. When it comes to the selection of CNC machining center accuracy, users have the ability to select machine tools that correspond to varying levels of accuracy. Because of this, users are able to select the accuracy of the CNC machining center in accordance with the requirements for machining accuracy posed by the workpiece. When it comes to mass-produced parts, the actual processed accuracy value can be anywhere from 1. 5 to 2 times higher than the positioning accuracy. Case in point Case in pointBecause CNC machining center manufacturers typically configure three to three and a half distinct capacities of tool magazines for the same type of machine tool, the choice of tool magazine capacity for CNC machining centers is determined by the fact that CNC machining center manufacturers offer a variety of tool magazines for their products. The number of tools that can be stored in the horizontal machining center's tool magazine, for instance, can range anywhere from 30 to 80 or even more. In the vertical machining center, the tool magazines have capacities of 16, 24, and 32, respectively, depending on the size of the tool.
The user is able to establish the necessary quantity during the selection process by referring to the outcomes of the process analysis performed on the workpiece that is being processed. This allows the user to determine what is required. The number of tools that are required for a single clamping of a part is typically what determines how much space a tool magazine has available for its contents. This is because in order to process one component, another component needs to have a clamp placed on it at the same time. It is essential to reorganize the tools because, without doing so, tool management will be challenging and prone to mistakes. Given the current state of affairs, it is self-evident that a response is required to the aforementioned question. It is recommended that the tool magazine capacity of the machining center machine tool that will be used in the flexible manufacturing cell (FMC) or flexible manufacturing system (FMS) be selected as a large-capacity tool magazine, or that the machine tool be equipped with an exchangeable tool magazine. Both of these options are available as part of the flexible manufacturing family of products. Because of this, it is not fiscally responsible to choose a large number of accessories without first determining what your ultimate goal is going to be. Trying to arrange one's thoughts in a logical fashion is essentially a waste of time. As a consequence of this, it is absolutely necessary to carry out an exhaustive analysis when selecting and placing an order, as well as to appropriately take into consideration long-term factors.

Describe in detail each of the four characteristics Sandblasting Services that set precision molds apart from other molds.
As a direct result of the lightning-fast advancement of precision molds, the precision mold industry in my country has already carved out a prominent position for itself at the forefront of the global market. The precision molds that are produced in my country currently have the following characteristics: resistance to wear, strength and toughness, performance under conditions of fatigue fracture, and performance under conditions of high temperature. High levels of wear and tear brought on by intense friction, which ultimately resulted in the mold becoming damaged beyond repair. Therefore, the mold's resistance to wear is one of the most fundamental and important properties, and the factor that affects the material's resistance to wear is the primary factor that determines the material's hardness. The quantity of carbides, their shape, size, and distribution, in addition to the type of carbides that are present in the material, are all factors that influence the wear resistance of the material.
The majority of the working conditions of toughness molds are extremely severe, and some of them frequently bear significant impact loads, which can lead to brittle fracture. This is because brittle fractures are more likely to occur when working conditions are extremely severe. In order to prevent the sudden brittle fracture of mold parts while the mold is being worked on, precision metal molds absolutely need to have a high level of both strength and toughness. The performance of the mold in terms of fatigue fracture is primarily determined by its strength, toughness, and hardness, in addition to the amount of inclusions that are present in the material. Case in point: Case in point: Case in point: CasWhen the working temperature of the mold is high, the mold's hardness and strength will decrease, which will lead to premature wear or, depending on the circumstances, the mold's plastic deforming and breaking.
Tags: Sandblasting Services
0 Comments